CFDMS
CFD Modelling and Simulation
Develop novel, advanced numerical methods and simulation tools to solve mesoscopic and macroscopic fluid dynamic problems.
In the CFD-MS group we develop novel multiscale models and high-performance simulation algorithms to describe the dynamics of simple and complex fluids from microfluidics up to macroscopic flow conditions.
We perform massively parallel simulations to solve complex flow problems that rise in a number of engineering sectors including environmental, chemical manufacturing, polymer/food processing and biomedical research. The simulation framework relies on selective hierarchical approaches using Lagrangian macroscopic methods (Smoothed Particle Hydrodynamics) at the continum level, stochastic techniques (Brownian Dynamics, Dissipative Particle Dynamics, Lagrangian Particle Tracking) on the microscales, as well as hybrid coupling schemes for efficient multiscale computations.
The main current focus is on complex particulate flows such as transport of polymeric, colloidal, cellular dispersions, porous and granular media. We study particle dynamics (deposition/sedimentation/erosion processes) in manufacturing and biomedical applications as well as, on a more fundamental level, we aim at the understanding of the link between the microstructure of complex fluids and their macroscopic rheological response for novel liquid-based materials.
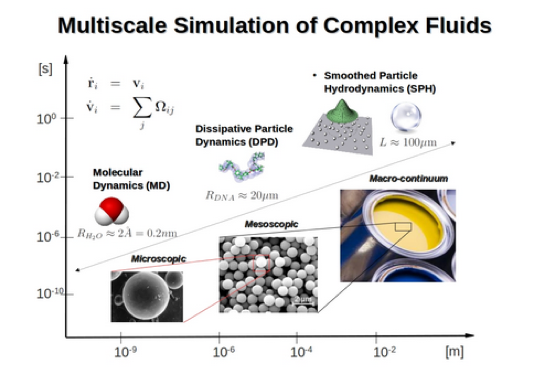
The current research lines of the CFD-MS group deal with the development and application of macroscopic and mesoscopic particle models for complex flow processes. Parallelization and optimization of the Lagrangian schemes is obtained by adopting routines for large-scale particle simulations, including the Particle- Particle-Mesh libraries (PPM). Here is a list of research topics:
CFD of viscoelastic fluids and elastic turbulence
The continuum flow of polymeric liquids through complex geometries is of paramount importance in many areas of engineering such as composite-polymer manufacturing, extrusion processes, lubrication, enhanced oil recovery but also for several biomedical applications. In most of these processes the appearance of non-linear instabilities of the complex fluid might affect drastically the dynamics, eventually leading to a chaotic unsteady state even in the absence of fluid inertia (zero Reynolds number): a phenomenon denoted as “elastic turbulenceâ€. In the area of biomicrofluidics, elastic instabilities triggering micro-turbulence have been recently exploited for the design of novel mixing devices operating with biological liquids, whereas in manufacturing engineering (e.g. polymer extrusion) elastic instabilities represent a source of artifacts to be avoided. Despite the large technological importance of the problem, the flow of highly elastic liquids through complex geometries remains controversial. The main issue is related to a typical sudden large increase in the flow resistance and unsteadiness which cannot be predicted based on existing models. SPH-based CFD computations of viscoelastic liquids [1] through a periodic channel flow have provided evidence of unsteady elastic behaviour and enhanced resistance, in quantitative agreement with experimental observations and theoretical predictions of the energy spectrum [2]. Simulations indicate that for a sufficiently large level of fluid elasticity, a chaotic self-sustained state corresponding to inhomogeneous near-wall structures of polymer over/under-extension (Fig. 1, top/right), can be established where enhanced mixing of mass takes place (Fig.1, bottom). The objective of this research direction is to explore novel strategies to control micro-mixing based on elastic turbulence.
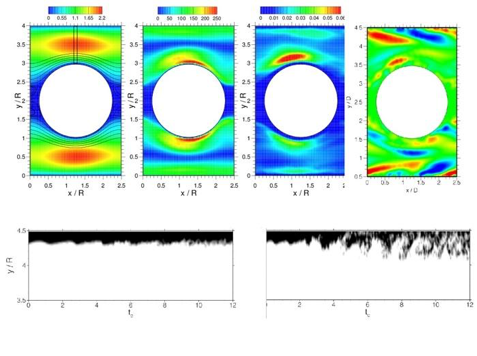
Fig. 1: Viscoelastic flow through a periodic array of cylinders. Top: a) steady mean velocity field (streamwise direction x); b) steady mean polymer conformation tensor (xx); c) Reynolds stress (xx); d) snapshot main unsteady mode conformation tensor (xx) obtained via Dynamic Mode Decomposition analysis Bottom: space-time diagram of mass mixing in the top near-wall layer with no elastic instability (left) and with instability (right) [2].
Computational Micro-Fluidics (CµF)
The increasing technological need to create and manipulate structures on micrometer scales and smaller has triggered the development of many numerical techniques for simulating flow problems at microscales. An emerging area is represented by bio-microfluidics where a single or a collection of molecules are actuated by accurate control of very small amounts of liquid (<ml) flowing through complex micro-devices. A challenging aspect in the modelling of complex fluids on these micro-scales (<<mm) is that no scale separation is present between the size of the suspended microstructure (e.g. the polymer molecule, colloid, cell etc.) and the external device, in such a way that no continuum model based on set of PDEs can be used. Instead, direct modelling of the microstructure, i.e. the dispersed phase, is required.
In our group we have developed a coarse-grained polymer-molecule model (Fig.2 left) where the Brownian solvent is described by the Smoothed Dissipative Particle Dynamics methods (SDPD) [3] which is a "thermodynamic-consistent" mesoscopic particle model of fluctuating hydrodynamics.
The current research direction is addressing virtual microfluidics-based rheometry (Fig. 2, right), where our recent mesoscopic simulations have allowed to clarify the link between the spatial flow relaxation of the complex liquid occurring along the channel with the microstructural relaxation processes of the single suspended polymers [4].

Figure 2: Top: mesoscopic model of a single polymer molecule suspended in a thermal solvent: microstructural properties [3]. Bottom: microfluidics-based rheometer: a polymeric fluid is injected into the left chamber and undergoes a sudden contraction. Mesoscopic simulations have been carried out to understand the link between microstructure changes and evolution of the macroscopic flow [4].
CFD and rheology of complex particulate systems
Accurate prediction of the dynamics and mechanical properties of micro/nano-particle suspensions interacting with complex media and under complex micro-flow conditions is critical for many industrial processes ranging from transport of slurries, seabed sediments to the design of hybrid particle-based fluids with enhanced shock-absorption performance, so called “shear-thickening fluidsâ€. In our group we have developed a new massively parallel mesoscopic particle simulation platform to characterize thermal and rheological properties of complex particulate systems based on SPH and SDPD. Starting from our validated mesoscopic models for colloidal and non-colloidal structures [5] suspended in simple Newtonian [6] (fig. 3: left) or viscoelastic matrices [7] (fig. 3, right), we are currently exploring the possibility to perform virtual rheology by means of direct numerical simulations (DNS) of new particle formulations, that is, by precise characterization of their input microstructure (particle shape, suspending medium rheology, microscopic inter-particle interactions etc.) to study quantitatively the corresponding bulk mechanical/thermal response. In particular, the main current focus is on shear-thickening fluids for novel hybrid fluid-solid materials with improved absorption properties.
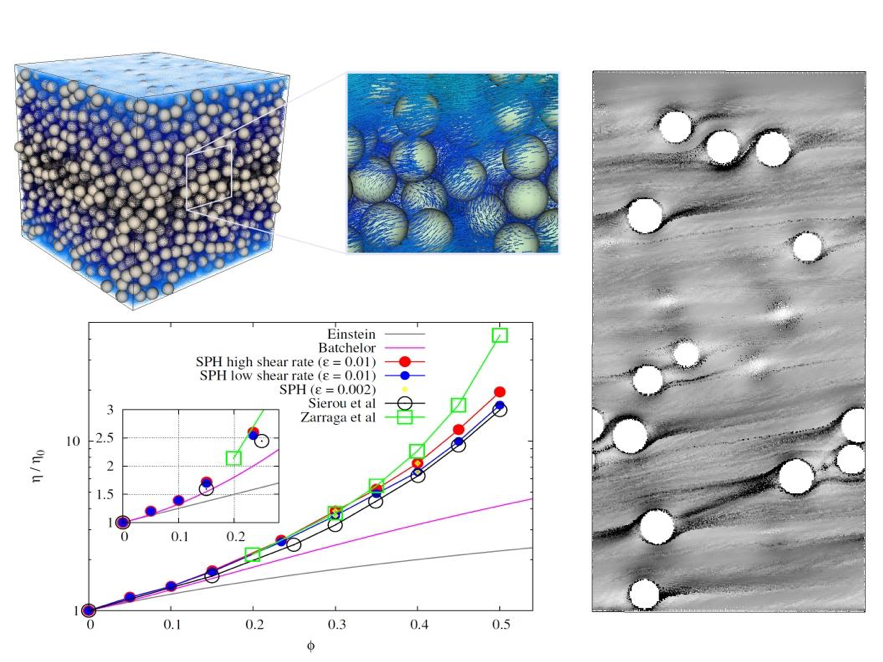
Fig. 3: Direct numerical simulation (DNS) of particle suspension rheology/dynamics. Left (top/bottom): suspension with a simple Newtonian solvent [6]. Right: suspension with a complex viscoelastic matrix (trace polymer conformation tensor shown).
Multiscale CFD modelling of biomedical flows
In many biological processes it is critical to predict accurately the cellular transport and deposition close to vessel walls in presence of a complex, unsteady flow. This is important to control drug delivery but also for the understanding of several cardiovascular diseases. Atherosclerosis, for example, is a degenerative disease of the arterial wall that is thought to be initiated due to inflammation of the arterial endothelium, promoting the over-deposition of white blood cells (WBCs). This anomalous WBC accumulation is site-specific and can lead to initial stage lesions or, on a long-term timescale, atherosclerotic plaques. To study these problems, we have recently developed a multiscale transport model for leukocytes [8] and coupled it to an endothelial cell receptor binding model in order to link the transport and surface biology [9]. The large-scale separation existing between biological components (order of microns) and typical vessel size in the macrovascular network (order of cm) prevents the use of detailed mesoscopic particle methods. The multiscale Lagrangian Particle Tracking (LPT) strategy proposed in [6] is based on a continuum viewpoint coupled with a discrete representation of the leukocytes as "test particles" rather than real cells. Leukocyte dynamics is handled based on a continuum advection-diffusion equation for a concentration field in the bulk domain, whereas discrete cells interacting with hydrodynamic and biological adhesion-mediated forces are considered in proximity of the vessel walls. The reduced number of tracked test particles which can be achieved by distributing them within a thin near-wall region only (Fig. 4 top) allow considerable speed-up of simulation for these systems, preserving the accuracy of the deposition profiles [9]. In [9] the multiscale model has been tested against in-vitro data from a 3D geometry with a stenosis and sudden expansion (Fig. 4 bottom). In both steady and pulsatile flow conditions, results show close agreement with the experimental ones considering a class of WBCs (U937 monocytic human cells) on a E-selectin-coated geometry. Future directions include the application of the current multiscale approach to in-vivo conditions such as the carotid bifurcations and other patient-specific flows.
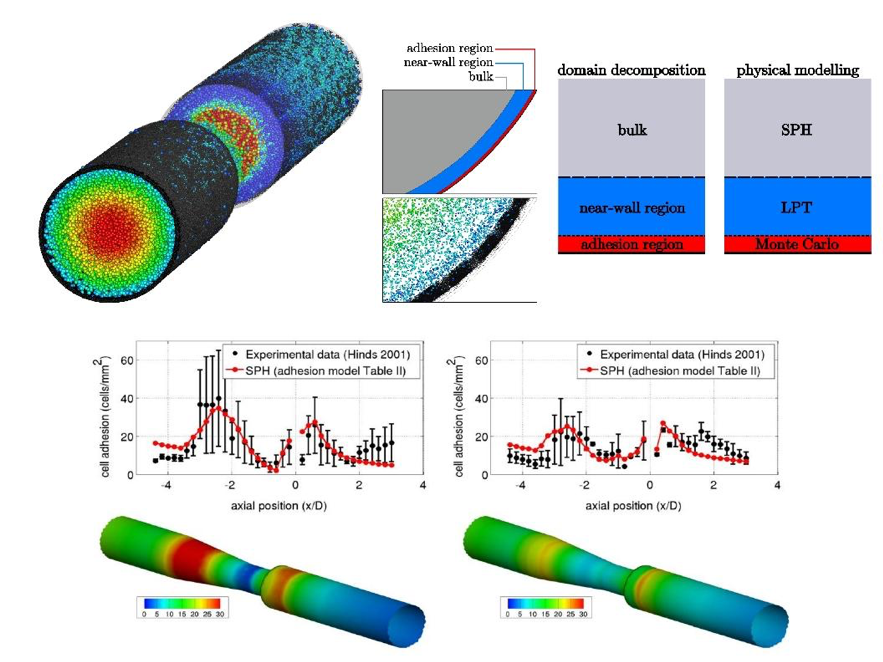
Fig. 4: Multiscale Lagrangian Particle Tracking (LPT) scheme for leukocytes in flow: (Top) leukocyte dynamics in the bulk is described by a continuum concentration field governed by an advection-diffusion equation; near-wall layer is filled with test particles undergoing detailed LPT with realistic lubrication and biologically-derived adhesionforces [8]. Bottom: comparison of cell adhesion data between simulation and the experimental data for U937 cells and E-selectin coated device surfaces to replicate mechano-chemical environment.
BBIPED: CFD Industrial Platform for Engineering Design
BBIPED (BCAM-Baltogar Industrial Platform for Engineering Design) is an engineering simulation software for fluid dynamics industrial applications [10]. BBIPED can handle a wide range of engineering applications in sectors such as turbomachinery, aeronautics, renewable energy, biosciences, advanced manufacturing, automotive, water and heat management; providing ad-hoc solutions for specific industry needs.
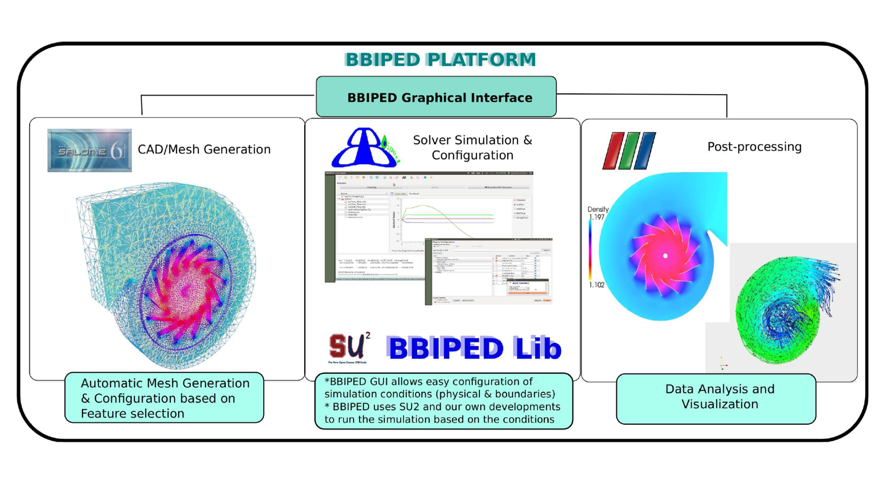
Fig. 5: BBIPED Platform Schema. The BBIPED Platform is composed by 3 main blocks (from left to right): CAD/Mesh generation, Solver configuration and simulation, and Post-processing. Each of the blocks are integrated through a common interface, the so-called BBIPED Graphical Interface(BBIPED GUI).
The BBIPED Graphical User Interface allows an automated CFD simulation process from CAD generation, meshing, solving and post-processing (Fig.5). The idea of developing this platform was proposed by BCAM and Baltogar, who joined efforts to overcome current industrial challenges in turbomachinery design by means of extensive research. This work has been developed within the research project "Development of an efficient, flexible and innovative CFD Computational Platform to optimally simulate and design industrial products and processes", co-funded by the Department of Economic Promotion of the Biscay Foral Council and the Department of Education, Language Policy and Culture of the Basque Government. In the recent project FRACTAL in collaboration with ETXE-TAR a CFD simulation of beam deposition process for a control laser device was performed [3]. The BBIPED Software was used to design and optimize a Laser-feeder cladding system and minimize lost material and processing time.
References
[1] Ellero, M. and R. Tanner (2005). SPH simulations of transient viscoelastic flows at low Reynolds number. Journal of Non-Newtonian Fluid Mechanics 132(13), 61 –72.
[2] Grilli, M., A. Vazquez-Quesada, and M. Ellero (2013). Transition to Elastic Turbulence and Mixing in a Periodic Channel Flow. Phys. Rev. Lett. 110, 174501(5).
[3] Litvinov, S., M. Ellero, X. Hu, and N. A. Adams (2008). Smoothed dissipative particle dynamics model for polymer molecules in suspension. Phys. Rev. E 77 (6), 066703.
[4] Litvinov, S., X. Hu, M. Ellero, and N. A. Adams (2014). Mesoscopic simulations of the transient behaviour of semi-diluted polymer solutions in microchannel following extensional flow. Microfluids and Nanofluidics 16(1), 257–264.
[5] Bian, X., S. Litvinov, R. Qian, M. Ellero, and N. A. Adams (2012). Multiscale modeling of particle in suspension with smoothed dissipative particle dynamics. Physics of Fluids 24(1), 012002, 012002.
[6] Vazquez-Quesada and M. Ellero (2016). Rheology and microstructure of non-colloidal suspensions under shear studied with Smoothed Particle Hydrodynamics. Journal of Non-Newtonian Fluid Mechanics 233, 37–47.
[7]Vazquez-Quesada, A. and M. Ellero (2017). SPH modelling and simulation of spherical particles interacting in a viscoelastic matrix. Physics of Fluids 29, 121609–12.
[8] Gholami, B., A. Comerford, and M. Ellero (2014). â€A SPH multiscale particle model of the near-wall dynamics of leukocites in flowâ€. Int. J. Num. Meth. Biomed. Engng. 30, 83–102.
[9] Gholami, B., A. Comerford, and M. Ellero (2015). SPH simulations of WBC adhesion to the endothelium: the role of haemodynamics and endothelial binding kinetics. Biomechanics and Modeling in Mechanobiology 14(6), 1317–1333.
[10] Carmen Alonso-Montes, I Garcia, A Ramezani, L Remaki (2014) BBIPED: BCAM-Baltogar Industrial Platform for Engineering Design International Conference on Circuits, Systems, Communications and Computers (CSCC 2014); Advances in Engineering Mechancis and Materials, Proc. the International Conference on Industrial Engineering (INDE 2014).
Snapshots location for Reduced Order Models: An approach based on Proper Orthogonal Decomposition and Mesh Adaptivity Techniques
On Adomian Based Numerical Schemes for Euler and Navier-Stokes Equations, and Application to Aeroacoustic Propagation
BBIPED
CFD Industrial Platform for Engineering Design
News! BBIPED platform beta has been released !. Download
If you have windows, you can still try it by means of VirtualBox. Here, you can download a virtualbox with everything ready. Try it! BBIPED-VirtualBox
BBIPED is an engineering simulation software for fluid dynamics industrial applications. BBIPED can handle a wide range of engineering applications in sectors such as turbomachinery, aeronautics, renewable energy, biosciences, advanced manufacturing, automotive, water and heat management; providing ad-hoc solutions for specific industry needs.
The BBIPED Graphical User Interface allows an automated CFD (Computational Fluid Dynamics) simulation process from CAD generation, meshing, solving and post-processing.
The idea of developing this platform was proposed by BCAM and Baltogar, who joined efforts to overcome current industrial challenges in turbomachinery design by means of extensive research. Thus, BBIPED is the result of a fruitful collaboration between science and industry. This work has been developed within the research project "Development of an efficient, flexible and innovative CFD Computational Platform to optimally simulate and design industrial products and processes", co-funded by the Department of Economic Promotion of the Biscay Foral Council and the Department of Education, Language Policy and Culture of the Basque Government.
BBIPED Key Features
- A friendly user GUI (easily customizable on demand) is provided to better manage the CFD workflow process from CAD, to solving and post-processing
- Ad-hoc solutions to fit industrial needs keeping the same interface, reducing engineers learning curve
- Flexible easy to use for engineers, showing only what they need (customizable configuration variables views)
BBIPED Extra Features
- Highly customizable eXtended SU2 (XSU2) library for future developments
- Multi-zone computation
- Multiple rotating reference frame: using multizone or virtual zone approaches
- Improved boundary conditions for internal flows.
- Customized CAD parametrization for automatic optimization
- CAD-free flow simulation
BBIPED Research Roadmap
- Multiphysics
- Proper Orthogonal Decomposition (POD) and Genetic Algorithms (GA) for optimization
- New turbulent models
- Medical Applications
Our partner
We would like to thanks the effort and support of our main partner in this project, Baltogar
Co-funded by
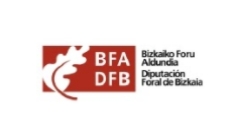
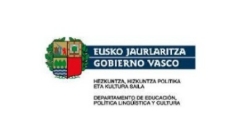
Acknowledgments
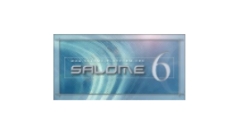
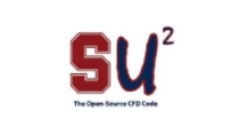
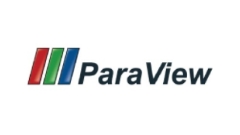
Download Links:
BBIPED
Plataforma Industrial CFD para el diseño de Ingeniería
Noticias Acaba de lanzarse la plataforma beta de BBIPED Descargar
Si tiene instalado Windows, todavía puede probarlo a través de la VirtualBox. Aquí se puede descargar un VirtualBox con todo preparado. ¡Pruébelo! BBIPED-VirtualBox
BBIPED es un software de simulación de ingeniería para aplicaciones industriales de dinámica de fluidos. BBIPED puede gestionar una amplia gama de aplicaciones de ingeniería en sectores como la turbomaquinaria, aeronáutica, energías renovables, biociencias, fabricación avanzada, automoción y gestión del agua y del calor, proporcionando soluciones ad-hoc para necesidades específicas de la industria.
La interfaz gráfica de usuario BBIPED permite automatizar el proceso de simulación de dinámica de fluidos computacional (CFD), a partir de la generación de CAD, al mallado, la resolución y el postprocesado.
La idea de desarrollar esta plataforma fue una propuesta de BCAM y de Baltogar, que aunaron esfuerzos para superar los retos industriales actuales en el diseño de turbomaquinaria a través de una investigación exhaustiva. Así, BBIPED es el resultado de una fructífera colaboración entre la ciencia y la industria. Este trabajo se ha desarrollado dentro del proyecto de investigación «Desarrollo de una Plataforma Computacional de CFD eficiente, flexible e innovadora para simular y diseñar óptimamente productos y procesos industriales» y ha sido cofinanciado por el Departamento de Promoción Económica de la Diputación Foral de Bizkaia y el Departamento de Educación, Política Lingüística y Cultura del Gobierno Vasco.
Principales prestaciones de BBIPED
- Se proporciona una interfaz gráfica del usuario fácil de usar (fácilmente personalizable bajo demanda) para mejorar la gestión del proceso de flujo de trabajo CFD desde el CAD y hasta la resolución y el postprocesamiento.
- Soluciones ad hoc para adaptarse a las necesidades industriales manteniendo la misma interfaz, lo que reduce la curva de aprendizaje de los ingenieros.
- Es flexible y fácil de usar para los ingenieros, ya que solo muestra lo que necesitan (vistas de variables de configuración personalizables)
Prestaciones extra de BBIPED
- Biblioteca eXtended SU2 (XSU2) altamente personalizable para futuros desarrollos
- Cálculo Multi-zona
- Múltiples marcos de referencia rotativos: uso de enfoques multizona o de zona virtual
- Condiciones de frontera (contorno) mejoradas para flujos internos.
- Parametrización personalizada de CAD para optimización automática
- Simulación de flujos sin CAD
Hoja de ruta de investigación BBIPED
- Multifísica
- Descomposición ortogonal adecuada (POD) y algoritmos genéticos (GA) para la optimización
- Nuevos modelos turbulentos
- Aplicaciones Medicas
Nuestro socio
Queremos agradecer el esfuerzo y el apoyo de nuestro principal socio en este proyecto: Baltogar
Cofinanciado por
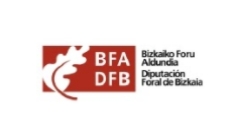
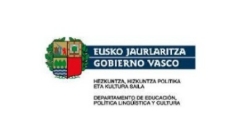
Agradecimientos
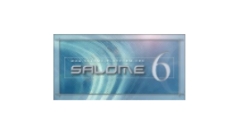
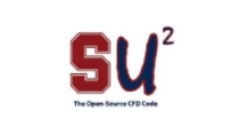
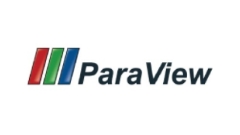
Descargar enlaces:
BBIPED
CFD (fluidoen dinamika konputazionala) plataforma industriala ingeniaritza diseinurako
Berria! BBIPED plataformaren beta bertsioa abian da! Deskargatu
Windows erabiltzen baduzu, proba ezazu VirtualBox baliatuta. Hemen deskargatu dezakezu VirtualBox, erabat prest. Proba ezazu! BBIPED-VirtualBox
BBIPED fluidoen dinamikaren aplikazio industrialetarako ingeniaritza simulazioak egiteko softwarea da. BBIPED softwareak ingeniaritzako aplikazioen sorta zabalarekin lan egin dezake askotariko sektoreetarako, esaterako: turbomakinak, energia berriztagarriak, biozientziak, fabrikazio aurreratua, automobilgintza, ur eta beroaren kudeaketa, etab. Honela, ad-hoc irtenbideak eskaintzen ditu sektore bakoitzeko behar espezifikoetarako.
BBIPED erabiltzailearen interfaze grafikoak CFD (fluidoen dinamika konputazionala) simulazio automatizatu bat ahalbidetzen du: CAD sorrera, engranajea, ebazpena eta prozesamendu ondorengoa.
Plataforma hau garatzearen ideia BCAMena eta Baltogarrena izan zen eta, ondorioz, buruz buru lan egin zuten turbomakinen diseinuaren arloko gaur egungo erronka industrialak gainditzeko, ikerketa sakonen bitartez. Beraz, zientziaren eta industriaren arteko lankidetza oparo baten emaitza da BBIPED. Lankidetza hori Bizkaiko Foru Aldundiko Ekonomia Sustapenerako Departamentuak eta Eusko Jaurlaritzako Hezkuntza, Hizkuntza Politika eta Kultura Sailak batera finantzatutako “CFD plataforma konputazional efiziente, malgu eta berritzaile baten garapena produktu industrialen simulazio eta diseinu optimorako” ekimenaren esparru barruan garatu da.
BBIPED softwarearen ezaugarri nagusiak
- Erabiltzaile interfaze grafiko erabilerraza (erraz pertsonalizatu daiteke) eskaintzen du CFD lan prozesua (CADetik hasi eta ebazpen eta prozesamendu ondorengo fasera arte) hobe kudeatzeko.
- Ad-hoc interfazeak, behar industrialetara egokituak, betiere interfaze bera mantenduta eta ingeniarien ikasketa kurba murriztuta.
- Malgua eta erabilerraza ingeniarientzat; behar dutena bakarrik bistaratzen du (konfigurazio aldagai pertsonalizatuak dituzten ikuspegiak)
BBIPED softwarearen ezaugarri gehigarriak
- eXtended SU2 (XSU2) bilduma oso pertsonalizagarria etorkizuneko garapenetarako.
- Eremu anitzeko informatika.
- Erreferentzia esparru birakari anitza: eremu anitzak edo eremu birtualeko planteamenduak erabilita.
- Muga baldintza hobetuak barne fluxuetarako.
- CAD parametrizazio pertsonalizatua optimizazio automatikorako
- CAD gabeko fluxu simulazioa
BBIPED ikerketaren ibilbide orria
- Multifisika
- Berezko deskonposizio ortogonala (POD) eta algoritmo genetikoak (GA) optimizaziorako
- Eredu turbulentu berriak
- Aplikazio medikoak
Gure bazkidea
Ahaleginagatik eta emandako laguntzagatik eskerrak eman nahi dizkiogu proiektu honetan gure bazkide nagusia izan denari: Baltogar
.Baterako finantzaketa
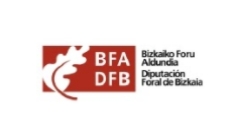
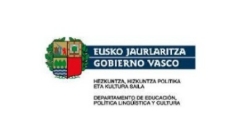
Eskerrak
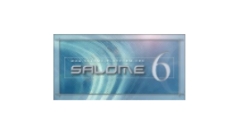
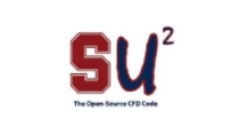
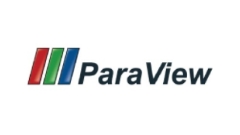
Deskargatzeko esteka:
BBIPED-GUI
Qt-based GUI for BBIPED. It integrates 3rd party software ( Paraview, Salome) and it provides an automatic configuration of CFD problems for their simulation using BBIPED-CORE
Authors: Carmen Alonso
License: LGPLv3.0
Placement
BCAM repository (redmine) - CFD-MS
BBIPED-CORE
It is a general Finite Volume code for simulation of wide range of applications such as: Aerodynamics and gas dynamics, water and liquid fluid flow, Turbomachinary. It has been the main CFD solver of the group since 2013 and some industrial projects have been accomplished in turbomachinary, renewable energy and wave energy sectors. The code is based on an old stable version of Su2 code (2.0.8) from Stanford university which is significantly has been changed in terms of new added features and several bug fixings.
Authors: Ali Ramezani, Goran Stipcich
License: LGPL
Mesh Converters
Currently available through BBIPED-CORE. Salome is one of the best open-source CAD and Mesh generator softwares that is widely used in research communities. To take advantage of this code we needed to generate .su2 extension for BBIPED. ExportSU2FromSalome.py is a script based code which must be run inside Salome in generate .su2 file directly from the generated mesh. Other converters such as .su2 to .med or .vtk and .vtk to .med are also available in SU2Converter.py and VTKConverter.py
Authors: Imanol Garcia
Lincense: LGPLv3.0 (same licence as BBIPED)
Placement
BCAM repository (redmine) - CFD-MS – Inside BBIPED-GUI and BBIPED CORE
BBIPED-GUI
Qt-based GUI for BBIPED. It integrates 3rd party software ( Paraview, Salome) and it provides an automatic configuration of CFD problems for their simulation using BBIPED-CORE
Authors: Carmen Alonso
License: LGPLv3.0
Download from
BCAM repository (redmine) - CFD-MS
BBIPED-Web
A simplified web-based GUI for academic purposes to be used in courses, avoiding OS dependencies, and connected to BCAM server resources. This is a result of a final Master thesis (supervised by Carmen Alonso Montes) - Already finished
Authors: Antonio Fernández de Rojas
License: LGPLv3.0
Download from
BCAM repository (redmine) – CFD-MS – BBIPED Web. Provided full source code to IT System.
https://projects.bcamath.org/attachments/download/212/BBIPED-Web-Platform-v0.1.zip